Why Proofing Matters
Authors: John Rastetter and Jeff Ashburn
The importance of color and the need for accuracy of reproducing color in packaging today cannot be overstated. The increase of brands in our market means that colors must match perfectly in order to maintain buyer recognition and loyalty. The only way to accomplish this goal of color consistency is to focus on ink standards and ensure that the package on the grocery store shelf matches the targeted color regardless of the type of substrate. After all, it is the identity of the brand being represented on that package, so perfection is the only option.
Of course, we all know that perfection isn’t always the outcome. Challenges occur along the way that interfere with our goals. Because of this harsh reality, it is necessary to deepen our understanding of ink and how to achieve that ideal color. In this paper, we will investigate the means of achieving color consistency in any situation through the use of ink proofing. To do so, we will cover the steps involved in ink proofing and discuss its importance to print. We’ll also include a special focus on Iris, Pamarco’s automated proofer, and explain how it can help you get the color you want with every print job.
When focusing on the significance of hitting color targets on all substrate types, it helps to think about brands that have mastered the skill of consistently recognizable color. A global brand must have consistent color regardless of the manufacturing location, and their packaging must be produced using the same formula and action steps. There must be accurate reproduction on a variety of substrates, on multiple types of equipment, run by varying people, using many different processes in all types of environments. With that kind of laundry list, how does anyone manage to get repeatable results?
Before we dive into the specifics of accurate reproduction, let’s begin in the shallow end with a quick review of the moving parts behind ink. The first priority is that ink must arrive at press side ready to run: that means meeting the LAB, dE and density requirements. All ink manufacturers have quality control procedures that include ink proofing technology, allowing them to meet brand owner requirements for color. The printer receiving the ink also has proofing technology to ensure the correct color match on site. But what happens when ink proofing procedures are not followed or are not performed consistently?
When ink arriving at press side isn’t the correct color, printers find themselves with color density outside of the needed range. In other words, it becomes a problem detectable to the naked eye. Sometimes operators notice before it’s too late and are able to make adjustments. But press time is costly, so even minor changes can be an expensive undertaking. Waste of time, waste of substrate, waste of consumption…the list of possibilities is long, not to mention the customer relationship strain during a long press OK, and/or the rejection of the job entirely. Even just a few extra minutes of make ready time that is associated with ink can be very costly on an annual basis, especially when press time costs $600/$800/$1,000 an hour – that can quickly become an expensive proposition. Some figures for example:
4 jobs a day
5 minutes saved per job
Press time: $800/hr or $13.33/min
Annual savings: $97,000
In order to avoid these issues and to those annual savings, we need ink that is pleasing to the highly accurate instrument most of us innately possess: the naked human eye. For this reason, drawdowns to ensure quality have been a staple of ink manufacturers and in-house ink departments for years, but repeatability has been a struggle for just as long. The keys to achieving the highest quality ink are three-fold: density, LAB and Delta E (ΔE or dE) standards. We all understand density, but what are the other two and why do they matter to drawdowns?
Delta E is a metric for understanding how the human eye perceives color difference. It is the measure of change in visual perception of two given colors. The term delta comes from mathematics, meaning change in a variable or function. The suffix E references the German word empfindung, which loosely translates to sensation.
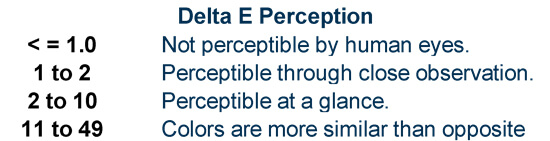